Pitch Your Capability Topic Week
By CDR Todd Greene
“It is very clear to me that logistics, among the warfighting functions, is the one that we need to make the most progress on right now…My number one focus is logistics, logistics, logistics.” –General David Berger, Commandant of the U.S. Marine Corps, May 23, 2023.
During a future conflict, the USMC may be operating multiple Expeditionary Advanced Bases (EABs) on dispersed islands across the Western Pacific. Within their respective island groups, the bases may reposition frequently to complicate enemy targeting. These EABs would either be established prior to the conflict while access was open, or they would be forcibly established with the joint support of naval assets fighting their way in. But naval support may not be accessible enough to provide steady logistical support to advance bases. This is an acutely challenging problem for EABs and demands innovation.
The USMC is aware of the logistics challenges accompanying their shift in doctrine against a peer adversary. There are many efforts to address the problem, but none cohesively solve it end-to-end. A solution is needed to address not only the challenges of long-distance contested transit across the open ocean, but also the last mile from sea to shore. A new, simple, and survivable system and its attendant concepts of operation could address these challenges and help provide consistent logistical support to stand-in forces.
Revising the Iron Triangle
Supplying widely distributed EABs of varying size, composition, and organic capability presents two sets of challenges – long-range transits across thousands of miles of contested open oceans, and last-tactical-mile delivery over an unimproved shoreline and into the hands of stand-in forces. Today’s systems mainly focus on one or the other, but there is nothing that can do both well.
Innovation must be directed at designing connectors that can bridge capability between these two distinct challenges. They must be able to transit oceanic spaces that feature hostile environments stemming from the open ocean environment and adversary capability. After traversing these many miles, the same system must somehow get supplies across a beach and into the hands of the stand-in force. Innovative connectors are necessary to provide the vital link between the stand-in forces and seabases or logistics hubs.
To help define the design of a new, innovative logistical connector it is important to first articulate and prioritize the system’s characteristics. Historically, a system that carries a payload is constrained by what is referred to as the “Iron Triangle” – range, speed, and payload weight. To increase performance in one area, the other two must suffer. Typically a tool cannot go fast and far while carrying a large load. Designers must pick one attribute to emphasize, or accept compromises across all. While these three traditional characteristics are still valid, the unique attributes of the transoceanic contested logistic problem leads to a revised iron triangle – efficiency, survivability, and cost.
Efficiency must be a driving consideration in any attempt to solve a problem when a cargo is being transported. Efficiency is often gauged by Freight Ton Efficiency (FTE), and measured in cargo ton-miles per gallon. When framed within the transoceanic lens, the optimized solution to move a variety of cargo already exists – the large containership. Unfortunately, a containership does not effectively meet the other two criteria.
By layering the additional need to not just cross an ocean, but cross a contested ocean, survivability must also be considered. The most efficient solution is no longer viable, since the typical containership is not survivable in wartime. Specifically, it is susceptible to targeting, vulnerable to attack, and does not have any ability to recover mission capabilities after suffering damage. Looking toward historic examples for design inspiration, the survivable solution to transoceanic contested logistics has historically been an escorted convoy.
The first two attributes of our revised iron triangle push the design solution for contested logistics in the direction of large commercial shipping, escorted for thousands of miles by an assortment of warships capable of providing area defense against a variety of multi-domain threats. The reality of available resources makes this a nonviable solution. By taking cost into consideration, the optimum solution becomes something simple, easy to build, and ideally shifts the enemy’s detect-to-engage calculus to where it becomes more expensive to find and kill the logistic system than the system itself. An example of a system matching this description is a simple steel barge.
The revised iron triangle is pushing for an innovation that features the best attributes of a containership, an escorted convoy, and a simple steel barge. How do we best combine these attributes and cross the shoreline?
Early Era Submarines and Narco-Subs
An emerging area of research being done at the Naval Academy and other facilities is in the specific hydrodynamic attributes of semi-submersible vessels (SSVs).1 This research has combined computational fluid dynamics, experimental tow tank testing, and parametric analysis of past and present examples.
Seagoing vessels are typically categorized as a surface ship, with the majority of the hull and superstructure existing and operating above the waterline, or as an undersea vessel that operates primarily completely submerged. A semi-submersible vessel is a hybrid that combines the properties of a surface ship and submarine to partially immerse, minimizing its above-waterline profile, while still remaining on the surface at all times. Yet only about 15-20 percent of a semi-submersible’s volume is above the surface.
In contrast to submarines, an SSV is dramatically simpler in both propulsion and structure. Due to its access to atmospheric air it can be propelled by standard internal combustion engines. It does not need to withstand high hydrostatic pressures since it does not dive, thus eliminating the costs to produce a vessel that can withstand oceanic pressure while submerged. It does not need control surfaces and mechanisms to maneuver sub-surface in three dimensions, further reducing cost.
By operating with a significant fraction of the hull submerged, the SSV differentiates itself from a surface vessel. Being in this semi-submerged regime has obvious advantages in reducing its observable signature. Additionally, there are significant wave-making resistance reductions, in the right conditions, discussed below.
World War I and II submarines frequently operated in a semi-submerged state, and a review of their operational and design parameters provides some instructive guidance for a modern SSV design. A statistical analysis revealed that significant operational advantages were realized in these early designs by optimizing the length to beam ratio and the speed to length ratio. A second, supporting parametric analysis was conducted on the only valid example of a semi-submersible operating in significant numbers today – the narcotics smuggling “narco-sub.” The results agreed with the early era submarine analysis and pointed to potentially advantageous design characteristics.
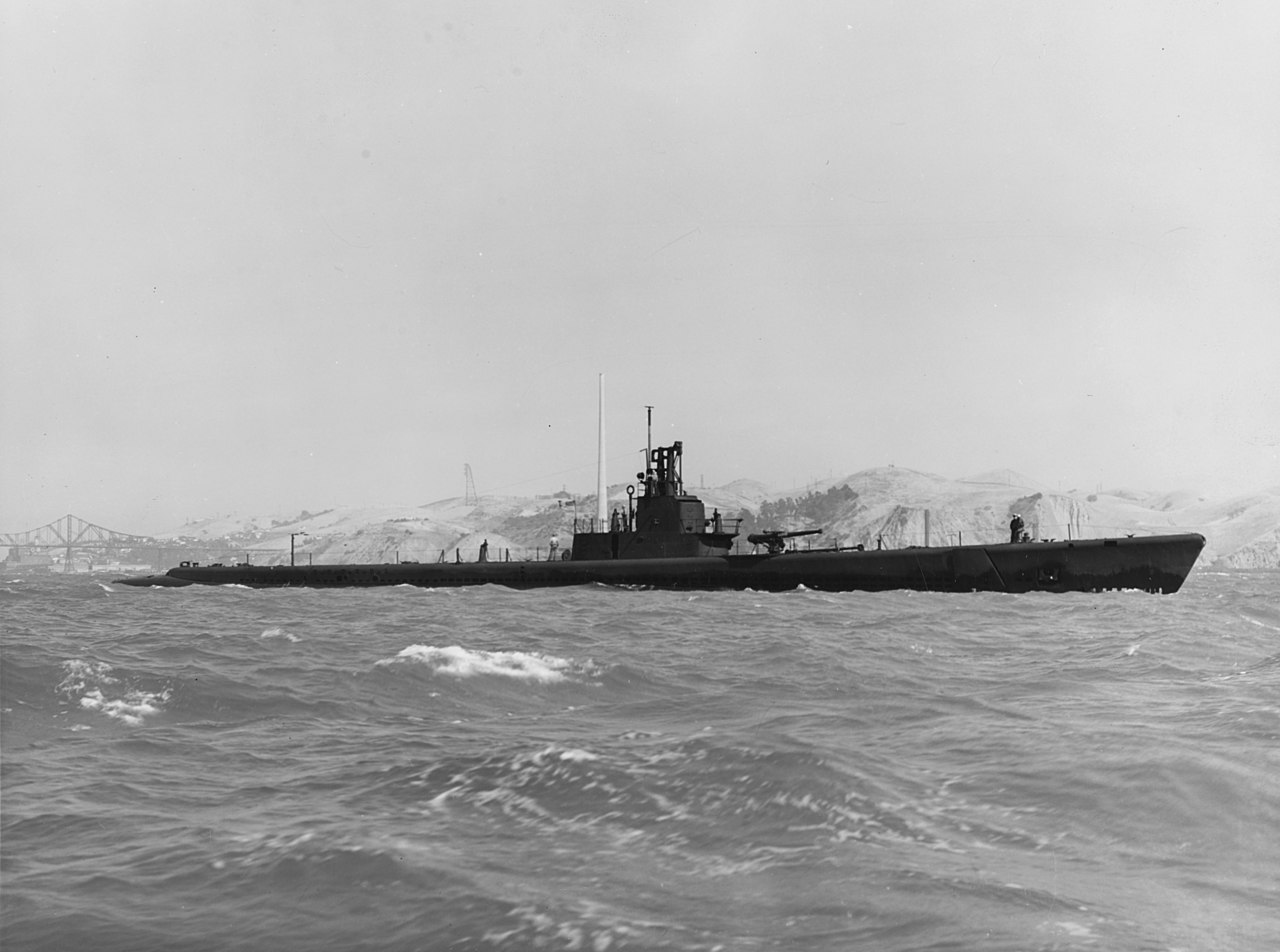
Using these historic and modern-day examples as a starting point, a set of computational and physical experiments were envisioned and conducted. The results of the experiments confirmed that there is indeed an efficiency advantage to be had by a semi-submersible if the SSV geometry is optimized and it is operated at the best speed.2 In other words, given two identical hulls, one operated primarily as a surface ship, the other operating semi-submerged, the semi-submerged hull can have less drag at the optimal speed.
With the knowledge that a SSV can be both more efficient and lower signature than a comparable surface vessel, the focus shifts to optimizing cost. If all three characteristics can be met, the foundation is laid for the next innovative contested logistics platform.
The Physics (and Beauty) of Shipping Containers
The intermodal shipping container needs no introduction. Nominally a rectangular container, measuring 20 feet in length, 8 feet wide and 8.5 feet high, is known as a TEU (twenty-foot equivalent unit). Many variations exist – 40-foot containers, 10-foot containers, Quadcons, High Cubes – but all retain the standard interfaces that allow them to be interchangeably loaded onto a ship, train, truck, and other forms of transport. The intermodal container is the innovation that unleashed the level of efficiencies now seen in transoceanic commerce. This innovation is very powerful in its end-to-end efficiency and must also be applied to optimize cost within the contested logistics problem.
The same characteristics that make the TEU containers valuable for peacetime commerce make them vital to solving contested logistics. The standardized sizes and interfaces not only make loading simpler, it means the material handling equipment to load, unload, and maneuver cargo is mature and universally available. When it comes to cost and production, shipping containers are not hard to acquire and they can be manufactured at many small-scale industrial facilities. Many existing military systems are already designed to be containerized and tens of thousands of containers are immediately available to DoD. Millions of containers are accessible in ports globally today.
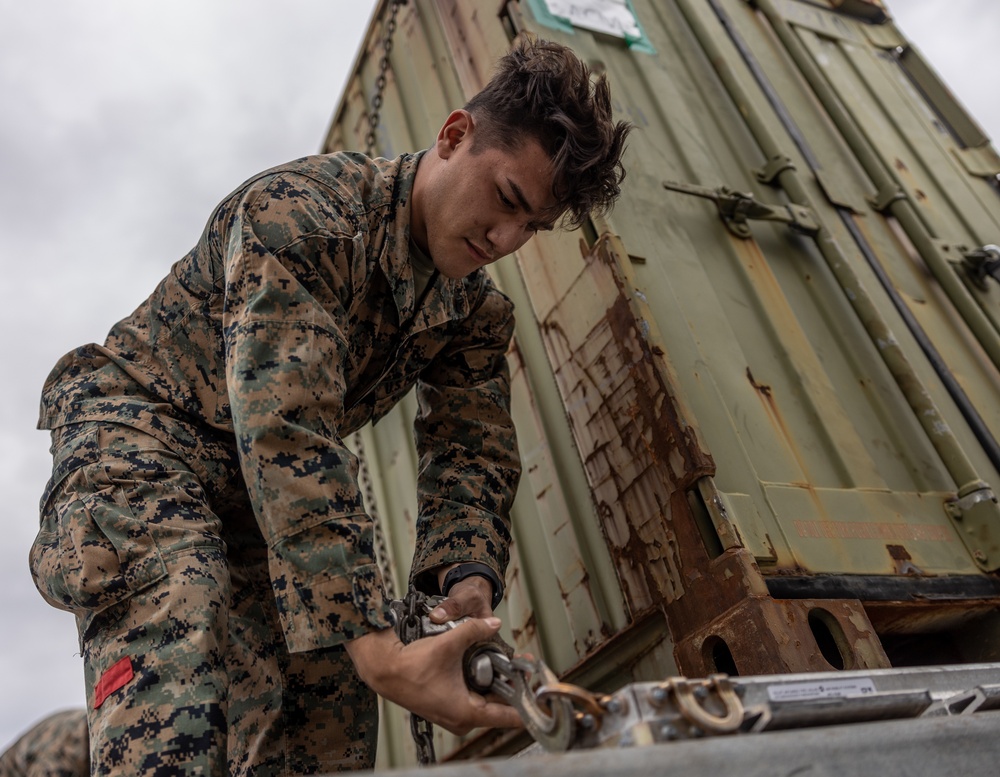
Unfortunately, it is not unheard of for shipping containers to be lost overboard. While not good for commerce, this gives us insight to another attribute that can be leveraged for innovation. Like a ship, a container that is immersed in seawater will sink to the point where the weight of water displaced by the container is equal to the weight of the container. This is known as Archimedes Principle. Hence, a fully laden 20-foot dry container will float for a time. This is because the volume of a 20-foot container is approximately 1,300 ft3. If it were to be fully immersed, it would produce about 83,000 pounds of buoyant force pushing it up, which is more than the 53,000 pounds of gross allowable weight of the container. Much like a semi-submersible, a fully loaded 20-foot container will therefore float with about 15-20 percent of its surface showing above the waterline, until it fills with water and sinks.
Containers come in many shapes and sizes, but only fit together in certain standard arrangements. Logisticians can choose the building blocks necessary to solve the contested logistic problem, while optimizing the freight ton efficiency, and ensuring compatibility with the receiving unit’s material handling capability. Building on conventional container variants, several unique container designs can optimize the opportunity presented by these systems.
- Commercially available containers (Figure 1):
- 20-foot TEUs – standard worldwide.
- 10-foot TEUs – same height and width as a 20-foot container, but half the length.
- “Quadcons” – same height and width as the 20-foot TEU, but a quarter of the length, and four fit in the footprint of one TEU.
- Unique containers envisioned for this system, featuring small departures from the current container variants (Figure 2):
- Half 20-foot – a standard 20-foot TEU split in two lengthwise, resulting in a container 20 feet long, 8.5 feet high, but only 4 feet wide.
- Buoyancy wedge – triangular prism with the same footprint as a Quadcon.
- Propulsion wedge – same dimensions as a buoyancy wedge, but with an installed battery-powered waterjet.
Figure 1: A sample of the standard, commercially available, container variants. (Left to right: Quadcon, 20-foot ISO container, 10-foot ISO container. Author graphic.)
Figure 2: Unique Containers envisioned for this system. (Left to right: Buoyancy wedge, Half-20-foot container, Propulsion wedge. Author graphic.)
Putting it Together: An End-to-End Solution
The system’s functional objective is resupply of distributed stand-in forces. The innovative contested logistic platform proposed is called NightTrain. It consists of an unmanned core semi-submersible, a strongback chassis, plus an assortment of standardized containers. The core vessel uses the hydrodynamic findings from the current and historic research to be optimized in shape and speed for long range transit across a variety of sea states, while being mostly submerged and therefore low-signature. It is autonomous and reusable, while housing the navigation and propulsion systems. It is attached to a cargo section through the strongback and propels the combined vessel.
Multiple cargo containers augment the core SSV. Arrangement of the containers is such that they link together to create the hull of the larger vessel. Loaded containers are placed on a standard commercial container trailer chassis. Like Legos, positioning pins on the trailer bed constrain the location of the containers into standardized arrangements. The loaded trailer is trucked from the warehouse to a port where the cargo containers are placed onto the strongback section of the NightTrain SSV. This strongback resembles a standard flatbed trailer. The consolidated NightTrain, with the forward two-thirds of its length being containerized cargo supported above the strongback, and the aft third being the propulsion system, is lowered into the water for departure or onto a mothership for further deployment.
This combination of containerized shipping technology and a semi-submersible hull meets our design goals of being efficient, survivable, and low cost. It features all the benefits of ISO standardized containers, including common loading, unloading, and material handling systems and interfaces. It exhibits hydrodynamically-optimized geometry and speed, providing for reduced resistance compared with a similar surface vessel. All system sub-components are over-the-highway transportable. The core SSV is a low-tech and affordable vessel that makes for a passively ballasted and traditional air-breathing diesel vessel that can meet the contested logistics challenge.
Crossing the Last Tactical Mile
The functional objective of this system is to deliver needed supplies into the hands of the stand-in forces while minimizing the specialized equipment and training required to process supplies on the receiving end. In many cases, setting a 20-foot container adrift a thousand yards off the beach is of zero practical value. In order to offer a true end-to-end solution, it must be able to cross the beach.
Imagine as the vessel approaches an EAB a certain number of the containers are released. The core vessel continues to the next EAB, and ultimately makes the round trip back to the logistic hub. The containers are released in navigable water just outside the surfline and cross the last tactical mile in one of three ways, depending on the organic capabilities of the stand-in force:
- Doorstep delivery via buoyant cache. The floating container is retrieved by the receiving unit using assets available to them (such as small boats or rotary wing aircraft), taking advantage of the container’s standardized connection points.
- Concealed delivery via subsea cache. The container is ballasted to sink when released. The position of the container is known by the receiving unit and combat divers can retrieve it. Buoyancy bags inside the container can be activated by the divers.
- Direct delivery via self-propelled containers. Standard containers are augmented by external propulsion containers (no larger than a five-foot Quadcon, Figure 3). These containers use a small water jet propulsion system to drive themselves onto a beach down a programmed line of bearing. This method may be reserved for only small units without any retrieval capability.

Illustrative Cases
Three scenarios are offered as illustrative cases across the spectrum of possible EAB logistical demand, demonstrating the versatility of the system.
EAB #1 – Marine Littoral Regiment (MLR/F-35 FARP)
Consider the challenges of resupplying an island similar in topology as San Clemente Island, but it is not conveniently off the southern California coast. Rather, the nearest major logistical node is more than 2,500 miles away. The island is about 50 square miles, with a primarily rocky coastline, and a small relatively shallow harbor with a pier capable of mooring barges and LCUs. This is a high volume, long-distance voyage. The most constraining logistical needs are: Class III: aviation fuel, and Class V: aviation ordnance. Fortunately, this EAB features organic capabilities that can help facilitate resupply. These retrieval assets include rotary wing aircraft, a small boat unit, heavy material handling equipment, and logistics personnel (Red Patch landing support, aviation ordnance techs, and refueling techs).
Operating from a nondescript warehouse near a commercial port in Guam, a Marine Corp logistics element receives the demand signal for 12,000 gallons of jet fuel as well as various aircraft repair parts. Two 20-foot containers are each loaded with a 6,000-gallon fuel bladder, and the bladders are filled. After being weighed, the logisticians fill one compartment of the buoyancy bladder in each container with compressed air, close the hatches, and load them on a flatbed container chassis using an overhead crane. Two additional Quadcon containers are packed with shrink-wrapped aircraft parts. These containers are also weighed and the buoyancy bags filled with air, then loaded on the trailer.
The loaded trailer (a 50-foot long combined load) is transported to the local port, lifted onto the waiting strongback, which is already attached to the core SSV. Using standard container hardware, the combined NightTrain SSV is lifted into the water, buoyancy is adjusted, diesels are started, navigation orders are loaded. It commences the 2,300 nautical mile journey to the EAB.
Approximately seven days later, having completed the contested oceanic transit, but unable to approach the island any closer than one nautical mile, the NightTrain SSV releases the cargo containers offshore. The containers float, and visual locator beacons are energized. Marines from the small boat unit, and CH-53Ks from the aviation detachment recover the floating containers. NightTrain transits back to the port where it was launched to refuel and reload.
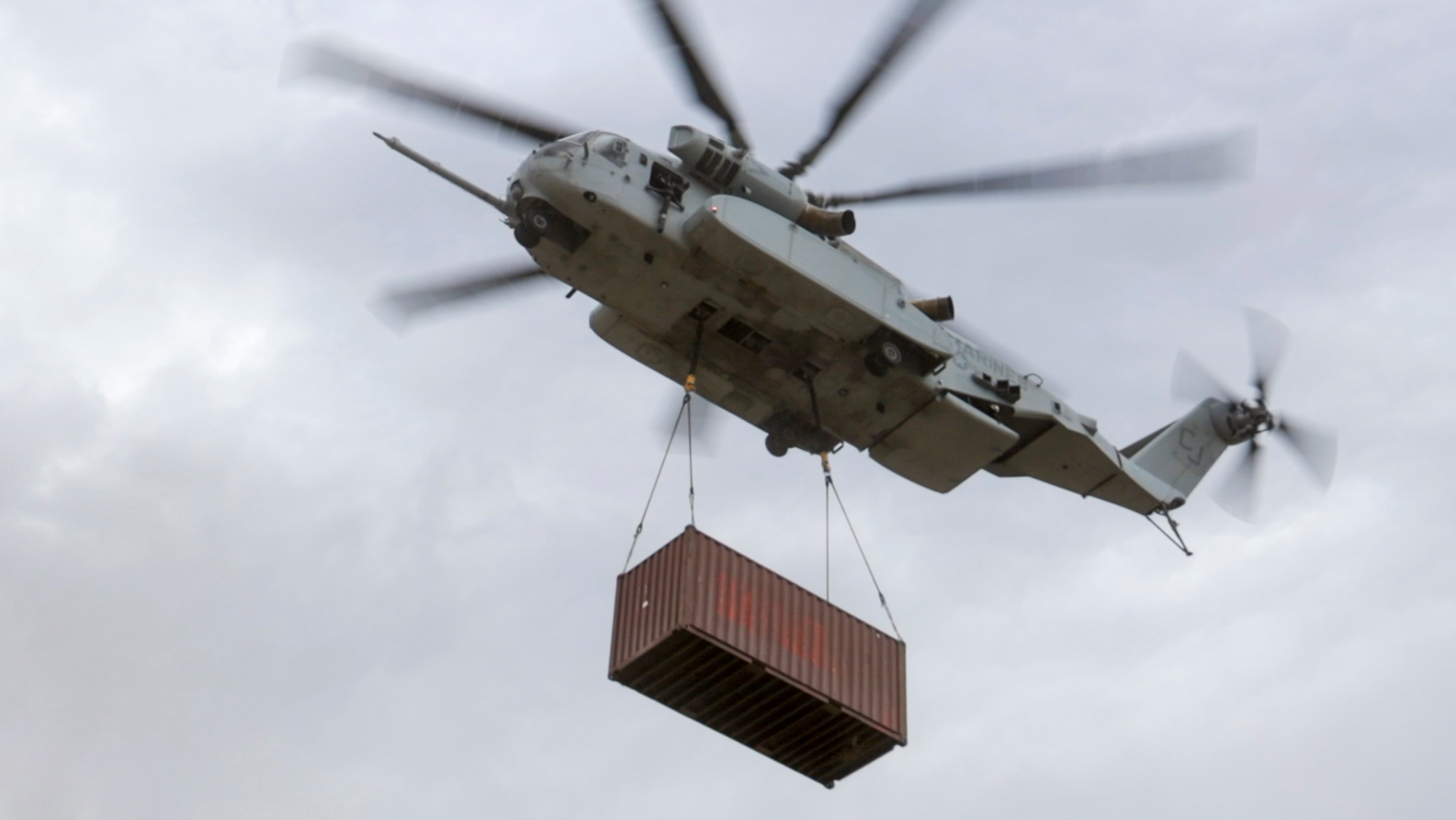
EAB #2 – Fires EAB (NMESIS detachment)
Consider an island similar to Snake Island in the Black Sea. While a tactically significant island, it is less than one square mile in area, without much cover. This island does have a short stretch of beach accessible by vehicle. The nearest logistical support node is about 100 nautical miles away. The most constraining logistical demand is Class V: ordnance, specifically canisterized Naval Strike Missiles. The only organic processing asset available on the receiving unit’s end are the NMESIS ordnance techs.
The logistical demand for eight canisterized Naval Strike Missiles is received at the logistics hub. Four “Half-20” containers are loaded with two shrink-wrapped NSM canisters each. After weighing the loaded containers and referring to the buoyancy table, the logisticians fill two compartments of the buoyancy bladders included in the container packout. The half-20s are loaded on a flatbed chassis. Four propulsion wedges are also loaded on the chassis, one attached to the end of each half-20. The total load is 50 feet long and eight feet wide. The trailer is taken to the port, mated with the NightTrain SSV, and launched.

Upon arrival in the vicinity of the island, all four half-20s are released, each with their own attached propulsion wedge. When afloat they settle on their sides, resembling a rectangular steel barge (20 feet long, 8.5 feet wide, and four feet deep). They are released southeast of the beach on the island and a quarter mile offshore. The electric propulsion units kick on, providing enough thrust and steering control to move the half-20 containers at four knots. The navigation system drives them down the magnetic bearing of 333 until they run aground on the beach. At that point, the NMESIS teams recover the containers with their vehicles, drag them up the beach, and retrieve the missile canisters. The batteries from the propulsion wedges are also recovered and repurposed.
EAB #3 – 6-man Force Recon Team
A recon team is tasked with ES observation using a passive ground-based sensor to provide targeting information to MLR area denial weapons. This unit is positioned on Koto (Xiao-Iam Yu) Island, adjacent to Orchid Island, approximately 40 nautical miles southeast of Taiwan. There are no improved facilities on the island, although it does have a protected sandy beach on its western side and is approachable to about 60 feet of water depth. The nearest logistical support node is between 200-500 nautical miles away. The primary logistical demands are Class III (fuel, 50 gal/day) and Class I. Organic resources available to the team to participate in resupply are just one rubber craft and combat divers.
Logistical demands for 100 gallons of diesel fuel and various food stores are predicted by the logistics depot. A single five-foot long Quadcon container is filled with the supplies and fuel. After being weighed, the logisticians fill three of the buoyancy compartments with water, none with air. A cylinder of compressed air is also attached to the buoyancy bag.
The Quadcon is included with a load of seven other quadcons on a trailer, taken to the port, and loaded onto the NightTrain SSV. The SSV makes the contested transit at 11 knots, stopping at five different waypoints along its way to release various canisters. When it arrives at the island, it releases the Quadcon 250 yards offshore, which sinks to the bottom in 80 feet of water. When ready, the Force Recon combat divers go to the location, dive on the canister, open the hatch, and activate the compressed air canister to float the supplies to the surface.
Ridesharing but for Expeditionary Bases
The rideshare model has shown its value versus the traditional centrally-dispatched taxi. A customer publishes their specific need and a decentralized fleet of suppliers evaluates their own ability to meet that need. The most optimally placed and capable supplier is automatically dispatched to meet the need.
Apply this concept now to our contested logistics problem. By using a combination of standardized and novel container types, many needs of all shapes, sizes, and capabilities can be supplied. There will certainly be many different demands and logistical capabilities of EAB customers. Using a system that allows a unit to publish their need (such as specific quantities of food and fuel) and their retrieval conditions and capability (e.g., rocky coastline, no improved port or protected beach, small boat unit), capable suppliers can self-nominate to fill the demand. This ultimately results in a distributed, resilient logistic network.
The innovative connector that makes this vision possible is an unmanned semi-submersible that serves to transport containers from the source of supply to the stand-in-force. This vehicle is efficient, survivable and relatively inexpensive. It leverages the best of modern logistical and hydrodynamic efficiencies. We call it the SSV NightTrain.
Commander Todd Greene, USN, is an Engineering Duty Officer serving as an naval architecture instructor at the U.S. Naval Academy. He is a graduate of the Naval Postgraduate School and the U. S. Naval Academy. The views and opinions expressed here are his own and do not necessarily reflect those of the U.S. Navy.
References
1. Sung, L. P., Matveev, K. I., Morabito, M. G. “Exploratory Study of Design Parameters and Resistance Predictions for Semi-Submersible Vessels.” Naval Engineers Journal, March 2023.
2. Sung, L. P., Laun, A., Leavy, A., Ostrowski, M., Postma, M., “Preliminary Hull-Form Design for a Semi-Submersible Vessel Using a Physics-Based Digital Model.” Naval Engineers Journal, December 2022.
Featured Image: A Rough Terrain Container Handler (RTCH) moving cargo. (USMC photo)
Sounds great combined with Prepo, Airland, Air delivery and small boats all possible sources. Key is whether forward deployed Marines actually means forward deployed. Additionally, does small groups of Marines = MEF, MEB AGTF, MEUs or platoons, squads, fire teams. Great things are expected from small groups when national survival at stake. Think Army three man units equipped with a hard to find jeeps and multiple Davy Crockett rockets. Or the MANPAD demolition munitions meant to buy time from a full on Warsaw pact assault. I see small groups of Marines with anti air anti ship missiles inside first island chain. Using fire and disperse to another pre built cache. This solution would have helped greatly during Philippine resistance period 1942-44.
Jai, thanks for the comments.
You don’t want a non standard cube for your last mile delivery. Maybe scale down the concept of a river containership. This concept is draft limited to start. Just keep it small, 1 container high, and with a ballast system. https://maritime-executive.com/article/u-s-shipyards-bidding-for-construction-of-hybrid-river-containerships
Andy, thanks for the comment. You are absolutely right about draft being the limiting factor for the last tactical mile. It’s back to the contradiction of needing to be mostly submerged to be survivable (and take advantage of the dip in resistance); but have a shallow draft if it is going to get across a beach.
This is what drove one of the last mile solutions to the “half-20.” This shape packs and ships like a standard TEU, but when launched it flips on its side, resulting in a draft of only about 3 ft. Additionally, it’s a one-way trip through the surf line, avoiding the problem of getting a ship off the beach.
Admittedly, I agree with you, any nonstandard cube is a disadvantage. The half-20 is a compromise to avoid added complexity of an active ballast system on an “inexpensive” autonomous system.
Of course the half-20 is only intended for the small receiving units with no ability to retrieve outside the surf line. Any unit with organic retrieval capabilities would receive a standard cube, waiting offshore.
I am very interested in your additional thoughts and feedback as we refine this conops and design.
Liking idea better. Balance between shipment surviving to last mile and then getting into hands of stay behind troops and allies. Thinking of WWII where small boats and seaplanes arrived at reef lines and then dropped barrels filled with supplies. Not anywhere near 100% effective but did enough. If your system is a robust enough way to supply/discharge things like HIMARs pods and current anti ship and anti air reloads effectively and efficiently enough to get past that last distance to the beach then it is a winner.
Thanks John. That is the vision.
We built a prototype for the Recon scenario years ago using IRAD money. We showed it to the USMC and they loved it but said they only had requirements for surface and ground systems—not modular amphibious systems. The system has been sitting in a warehouse for about six years. I have yet to find a DoD component funding this type of development though it solves a number of gaps common across all of the service branches. If anyone knows differently, please let me know who the POC is for this type of effort is. Thanks!
Thanks Johnny. I just sent you a separate note.